Aluminium has been long used within the automotive industry. It was first used exclusively for the frame of vehicles and has since gone on to play a much wider role, including within engines, chassis and other critical components.
Demand for using this material within the production of automotives continues on an upward growth trajectory. According to reports, the average vehicle will incorporate more than 230kg of aluminium by 2026, which stands at an increase of 12 per cent compared to the average figures in 2020.
With the introduction of new legislation in particular set to impact how vehicles operate and are manufactured, the use of aluminium is seemingly very much at the forefront of the automotive industry’s future.
How is aluminium currently used in the automotive industry?
The application of aluminium within the automotive industry is seen throughout the production of the vehicle. Its use can be split into two key areas: platform parts and component parts.
Platform parts relate more to the overall body of the vehicle. This comprises all the points of closure (such as doors, the bonnet and the boot), the chassis and the frame of the vehicle (such as the pillars and windshield frame). Importantly, aluminium is also used for a vehicle’s crash management system (CMS).
The component parts make up how the vehicle actually operates. Aluminium is often used within the powertrain (the system which makes the wheels on the vehicle turn), the transmission (which relates to the vehicle’s gearbox) and the vehicle’s heat management system. The material is also used as part of the brakes, steering and across the overall interior and exterior trim of the car.
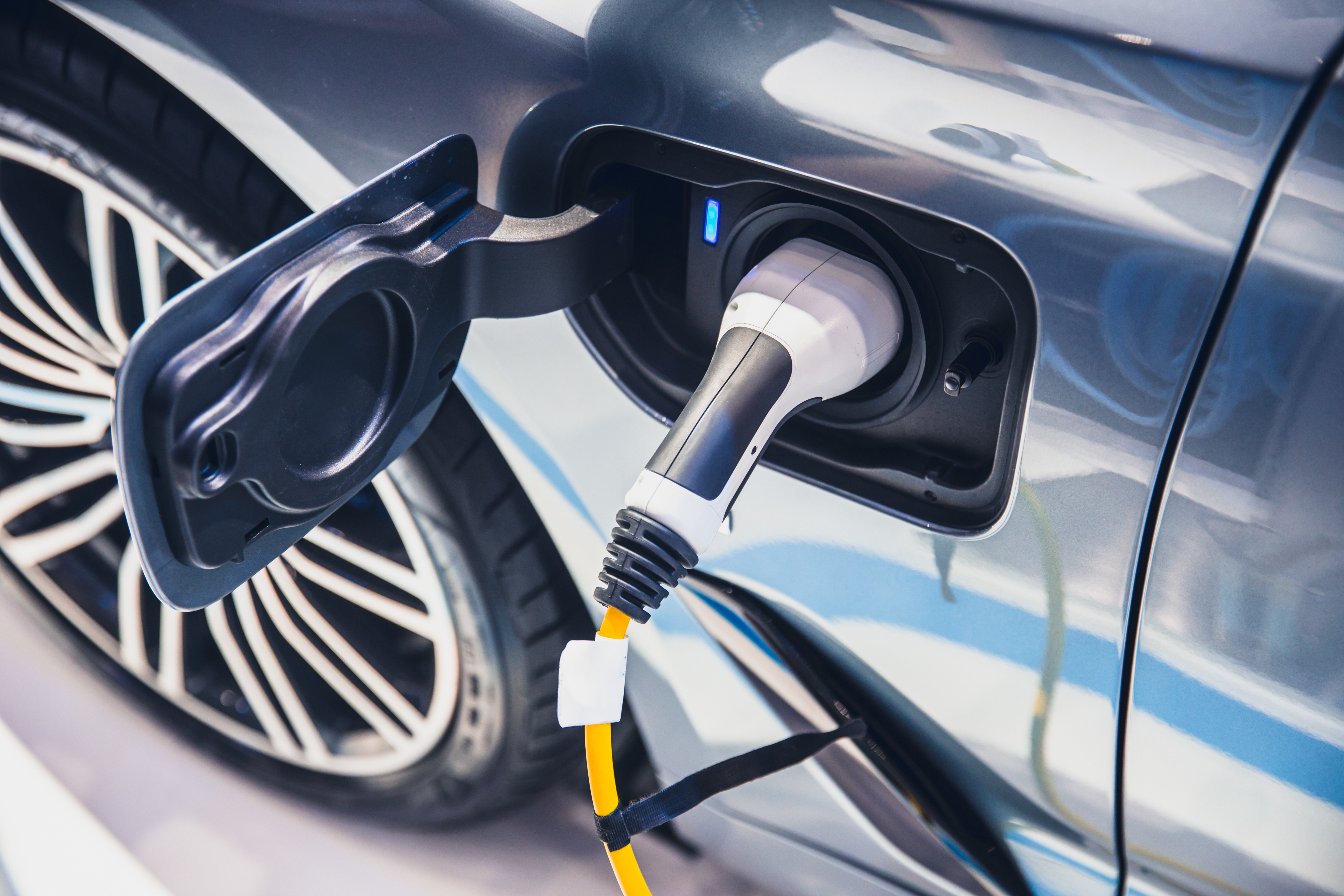
EV legislation driving the aluminium charge
The automotive industry has had the spotlight shined on it when it comes to reducing emissions which contribute to wider environmental issues. Emphasis is being placed on finding new sustainable solutions when it comes to vehicles, and legislation is driving change. In the UK, the sales of new cars and vans with petrol and diesel engines will be banned.
This makes electric vehicles (EVs) the future of the automotive industry. In 2012, 130,000 electric vehicles were sold globally – this figure is now at 6.6 million, an almost 5,000 per cent increase over the course of the last decade. The sale of EVs now makes up nine per cent of the global market share, its highest ever figure, and by 2030 this is expected to reach the 30 per cent mark.
However, with a move to EVs, the existing materials used within the vehicle’s production needs to be re-evaluated.
EVs do not have the same range capacity (i.e. how far they can drive) as a petrol or diesel powered car, due to limitations with the battery. This is hindered further when heavier, dense metals – such as steel – are used for the production of the vehicle, as it essentially weighs the car down and means more power from the battery is required to move it.
This is where the use of aluminium steps in. A lightweight material, which is durable, flexible and can easily be bonded, aluminium has become the material of choice for the industry. It also can enable the regulatory safety standards required for vehicles to be achieved, much like the heavier steel versions.
For EVs, aluminium is also used for components such as the housing and cables for the battery, as well as the traction motor, converter and gearbox housing.
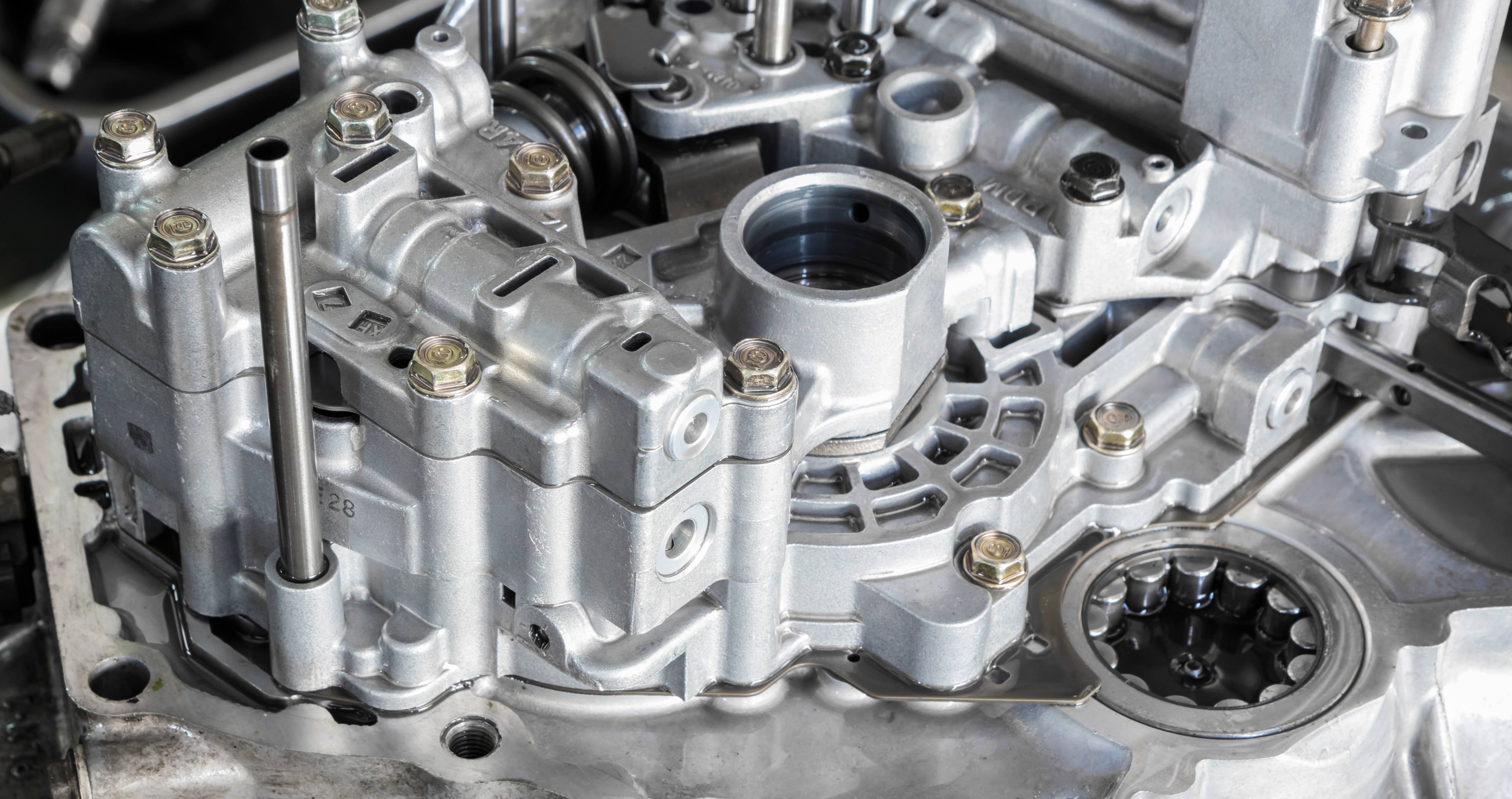
What are the key benefits of using aluminium in the automotive industry?
The use of aluminium within the automotive industry brings with it a range of benefits, from the overall performance improvements to its flexibility and malleability. Find out some of the key benefits below:
The lightweight alternative.
Aluminium is well known for being a lightweight metal, and is around a third of the weight of steel per cubic foot.
Performance attributes such as handling, breaking and acceleration can all be improved by using aluminium over steel, as the car is much lighter. The rigidity of aluminium also means drivers have much more precise and immediate control, which bolsters the overall performance.
Long-lasting.
Unlike steel, aluminium isn’t susceptible to rust and corrosion which is a huge benefit based on the weather conditions vehicles tend to be exposed to. Aluminium components also require less upkeep and maintenance and often have a much longer lifespan compared to alternative materials.
A more sustainable material choice.
The use of aluminium in the automotive industry is a more sustainable choice for manufacturers. Through opting for a fleet of aluminium vehicles over steel vehicles, more than 108 million barrels of crude oil can be saved and 44 million tons of CO2 emissions can be avoided.
Research also shows that more than 90 per cent of automotive aluminium is recovered for recycling at the end of a vehicle’s life, which helps keep with the material within a circular economy so it can be reused.
With the EV legislation on the horizon, opting for a more sustainable material choice for the manufacturing of the vehicles will help further push the automotive industry’s green agenda.
End user benefits.
Fuel is one of the biggest associated costs for drivers, especially in a time when petrol and diesel prices are at an all time high. The use of automotive aluminium can help save fuel compared to steel vehicles and improve the range of electric vehicles.
Safety is also a key benefit of using aluminium within the automotive industry. If a car crash occurs, aluminium can absorb twice as much energy as steel in the front and back crumple zones (i.e. where the impact is most likely to take place). This means safety can be bolstered without having to increase the overall weight of vehicle.
Aluminium: the past, present and future of the automotive industry
Aluminium has played a prominent role throughout the history of the automotive industry. As the next evolution of the sector starts to take place, the use of automotive aluminium is set to exponentially grow with the boom of EV manufacturing.
Being lightweight, durable and long lasting, aluminium is the perfect material to be used across a wide range of vehicle components and will only be used further in the manufacturing of vehicles in the coming years.